Pedana is a small town just 13 km from Machilipatnam, the Krishna district headquarters in coastal Andhra Pradesh. This small place has carved a niche for itself with its own style– Kalamkari textile materials.
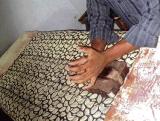
Over 1,000 artisan families survive on making vegetable dyes, blocks and printing of 25 distinctive Kalamkari textiles, including bedsheets, lungis, kerchiefs, curtains, Punjabi suits and sarees.
The Machilipatnam Kalamkari craft, made at Pedana, evolved with patronage of the Mughals and in the later years, the Golconda sultanate. “The word Kalamkari means, drawing with a pen. But our style is different from that of the Srikalahasti style or Pen Kalamkari,” says K Sudhakar, a second generation producer and trader of Kalamkari textiles in Pedana.
In Srikalahasti style, a pen is used for free hand drawing and then filled with colours. Deities and scenes taken from the great Hindu epics–Ramayana and Mahabharata–and the mythological classics, particularly the “Dasavataras”, are drawn on fabrics by hand. They employ the same method even for making paraphernalia used in temple festivals in southern India.
Artistes in Pedana use vegetable dyes and colours as they are pure and organic and have absolutely no side effects on users or the environment. Vegetable dyed fabrics and other items are more beautiful, popular and costlier than the regular products available in the market today. The reason is that it takes longer time and great effort to prepare vegetable dyes.
All vegetable colours are made using minerals, leaves, flowers and bark of different trees. For instance, distinctive red colour, a kind of trade mark for Kalamkari, is derived from a solution of alum and tamarind seed powder. Tamarind seed powder is boiled till it mixes well with water and then it is left to cool down to the normal temperature. The solution is then filtered using a muslin cloth. Alum works as the colour fixer for the solution.
Iron ore is used to make the black dye. The ore is powdered and boiled to make a solution. Process of cooling and filtering is involved while making all vegetable dyes. When the dye is ready, it is directly applied onto the pattern with a wooden block.
“For 20 kg of iron we use 15 kg of jaggery and 25 litre of water,” a worker at the Siva Aditya Handloom Textiles at the Brahma colony of Pedana says.
Similarly, violet colour is made out of natural indigo crystals. They are powdered and boiled to make a solution, yellow from turmeric and harad are used to make
yellow, mustard, lemon yellow and other tints and shades of yellow.
Along with buffalo milk, myrobalan is also used in Kalamkari. Myrobalan removes the odd smell of buffalo milk. The myrobolan can easily fix the dye or colour of the textile while treating the fabric. Alum is used in making natural dyes and also while treating the fabric. Alum ensures the stability of the colour in Kalamkari fabric.
The cotton fabric, made in powerloom with a certain weft and warf, comes mostly from Tamil Nadu and Maharashtra. All the 12 production units in Pedana buy cloth in huge quantities and distribute to workers who either take it up on a piece basis or work on weekly wages under a producer.
The wooden blocks are made as per the design given by the owner. “Generally the design made on paper is copied on the wooden blocks. Carving is done with improvised instruments made out of car valves, fan bearings and foundry equipment. I prefer rosewood as it is hard. Teakwood blocks wear off very fast. Also, carving needs special skills and patience,” says Madhusudan. After the printing is done with the help of these blocks, colours are put carefully. Later, the cloth is dipped in water for a while to help colours to get properly absorbed in the fabric.
From now onwards, the production of Machilipatnam Kalamkari is geographically limited to Pedana town and neighbouring villages of Machilipatnam, Polavaram and Kappaladoddi in Guduru mandal of Krishna district.
In August, the Machilipatnam style of art was registered in the Geographical Indications Registry (GIR) of the Government of India under the Geographical Identification of Goods (Registration and Protection) Act, 1999.
Members of Vegetable Dye Hand Block Kalamkari Printers’ Welfare Association, Pedana, have received the registration certificate from the GIR, Chennai. In the GI Registration, this art form has, however, been recognised as “Machilipatnam Kalamkari”. “The registration will enable us to initiate legal action against those who copy the art or design in any form. It also restricts the production of fabrics with Kalamkari art in the areas falling out of the registered geographical area,” says Welfare Association executive member B Anand Prasad.
The ingredients used in the preparation of colours, stages of applying the dye and designs on fabrics were also submitted to the GIR authorities for the conservation of the art as well as easy identification of violators anywhere. Nevertheless, the geographical identification was limited for a few areas of production – such as textiles and textile goods, bedsheets and table covers, clothing, carpets, rugs, linoleum and other materials for covering existing floors and embroidery.
The welfare association now has the right to seek legal action against those copying the art form of the registered products. On the one hand, efforts are being made by the Indian Council of Agricultural Research to produce new colours meant for Machilipatnam Kalamkari and, on the other, a special training programme on applying new colours was completed recently.
source: http://www.deccanherald.com / Deccan Herald / Home> Special Features / DHNS / Machilipatnam, JBS Umanadh – November 10th, 2013